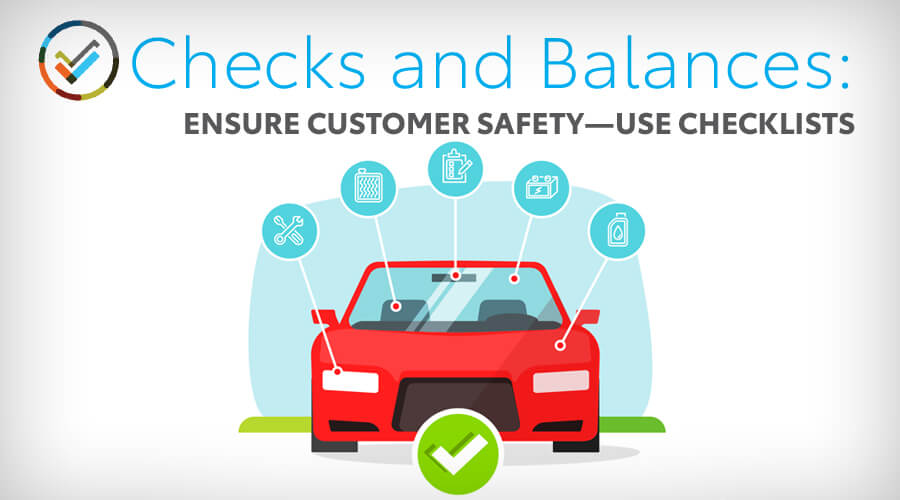
Checks and Balances: Ensure Customer Safety—Use Checklists
TOP PERFORMING SHOPS RELY ON FOCUSED PROCESSES TO MANAGE REPAIR DETAILS AND KEEP CUSTOMERS SATISFIED AND SAFE. One of the most frequently used processes is pre- and post-repair checklists to ensure all necessary repairs were properly performed.
When your customers take delivery of their vehicles after repairs are complete, they expect them to be in perfect operating order. If they find an issue, they can lose faith in both your facility and the vehicle itself. Pre- and post-repair checklists can be the key to a happy customer and future referrals. The following suggestions can help you create an effective checklist for your facility:
UPON ARRIVAL AT YOUR FACILITY:
Use a pre- and post-repair itemized check sheet. Best practice: Attach digital photos to the repair order to document the condition of the vehicle.
Conduct a thorough vehicle walk-around with the customer. Remind the owner that personalized electronic memory items may need to be reset once they take delivery, such as seat position, side mirrors, steering wheel, etc.
Record any non-related or pre-existing damage inside and out (digital photos of pre-existing conditions are helpful). Review your findings with the customer. Include a written consent form and explain that the vehicle will be test driven upon completion to validate all equipment is performing as designed.
BEFORE REPAIRS BEGIN:
Use a mil gauge to measure paint thickness when repainting is involved.
– This may also help identify if the vehicle has been previously worked on. Measure and check tires and note any abnormal wear pattern before beginning repairs. Check the 12-volt battery age and state of charge (sitting in a shop for an extended period without charging may drain the battery).
– Perform a pre- and post-scan (a health check) with Toyota’s Techstream or Techstream Lite to identify what past or current DTCs are listed and to see if any recalls or repair campaigns are needed.
– Use TIS vehicle inquiry to identify standard and optional equipment on the vehicle and to ensure correct parts
ordering.
Record settings of electronic memory of ECUs that can be reset without the owner, such as radio presets. Safely disarm the electrical system per TIS and print all TIS documents to know what’s involved in disassembly, non-reusable parts, precaution, inspection, dimensions and repair. Upon assembly include proper torquing of nuts and bolts, calibrations, or any other instructions or procedures needed to perform a complete and thorough repair.
Compare two- and three-dimensional measurements of the body structure and subframes. Measure and verify the geometric angles of steering and suspension components to validate that they’re within TIS specifications.
Look for predictable areas of misalignment that are engineered to deform, deflect and absorb collision damage away from the passenger cabin and minimize injury to passengers.
Look for holes, convolutions, punch-outs, kick up, kick down and laser-welded tailor blanks. Look for those not so obvious indicators of damage, like cracked paint or caulking, stressed or open seams, torn or broken welds, and loose or broken plastic components.
Inspect the engine compartment for bent or broken engine and transmission mounts, driveshafts and steering and suspension components.
Inspect the undercarriage for bent axles, suspension or steering components. – Check for fluid leaks on any moving components in the damage area, such as struts, steering assemblies, transfer case, rear axle, etc. Note: If an engine pan gasket is leaking, but there’s no visible damage, it may not be due to a collision.
Inspect the passenger compartment for secondary damage to interior components that are designed to absorb collision energy away from occupants to minimize injury. Check the vehicle for the Takata Airbag Recall: – toyota.com/recall/takata
Check for seat misalignment, binding, squeaks or rubbing while adjusting the seats. Inspect the seat belts for abnormal retracting, tears in the stitching or stretching, and anchor point deformations.
Inspect the steering wheel for abnormalities, such as bent spokes.
– Check if the steering wheel wobbles while rotating or if the front wheels aren’t pointing straight ahead when the steering wheel is centered. Turn the steering wheel completely right then completely left to identify any noises, binding or tight spots. Inspect the steering column for deformation.
– Locate the collapsing or break-away locations in “TIS New Car Feature” and “How to Inspect in the Repair Manual” section for each specific vehicle. Perform an Occupant Classification Sensitivity (OCS) inspection
using SST weights on the seats to measure accurate weight capacity for seats with sensors.
Inspect all lighting to see if front lamp aiming is needed.
AFTER REPAIRS ARE COMPLETE:
Conduct a post-scan health check to verify that all DTCs have been corrected.
Use the check-in checklist to verify that all equipment is functioning as designed.
Double-check the following:
– Paint looks like new.
– All bolts are tightened up.
– Air conditioning is fully charged.
– Fluids are topped off.
– Doors open, close, lock and unlock properly.
– Gaps and seams are aligned.
– The battery is charged, and the leads are on tight. Test drive the vehicle to confirm all systems are restored to pre-accident condition.
Finally, wash and clean the vehicle as if it were a new car delivery.
– Take post-repair digital photos and attach to the file.
You should also understand your customers’ rights when it comes to repairs.
When you take the time to properly check a vehicle in, and then review it again before delivery, your customers will know that you care about their business and their safety. Take the time and use checklists—your customers will thank you!
“After a vehicle has been in a collision, there can be many obvious and not obvious systems affected. All affected systems need to be repaired or replaced so the vehicle can look and perform as designed. If you overlook a system, and the vehicle is in another accident, customer safety may be compromised.”
— Joe DiDonato, Senior Collision & Refinish Training Administrator