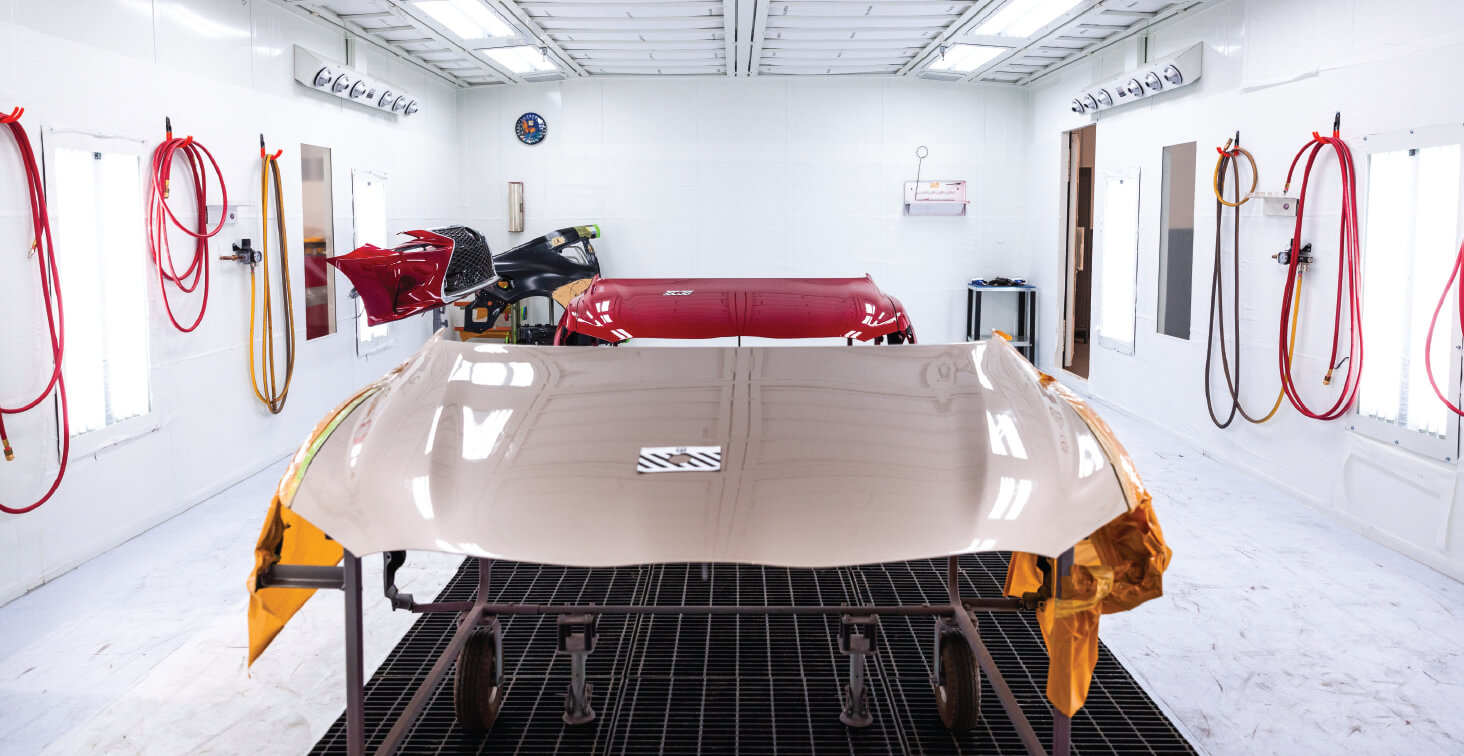
Collision Pros Magazine 2019 | ISSUE 2
Toyota’s New Collision Repair and Refinish Facility Opens in Rancho Cucamonga, CA
EXCITING NEWS! TOYOTA’S BRAND-NEW COLLISION REPAIR & REFINISH TRAINING CENTER HELD ITS GRAND OPENING ON APRIL 12, 2019.
The 11,000 square foot facility in Rancho Cucamonga offers collision repair and refinish training for both Toyota dealerships and affiliated independent collision centers. Replacing the Torrance location, this is the fourth Toyota Collision Training Center, along with facilities in Jacksonville, Florida; Plano, Texas; and West Caldwell, New Jersey.
HIGHEST QUALITY
Known for exacting standards, Toyota promises this facility will provide participants with the knowledge and skills they need to correctly and safely return vehicles to factory standards after a collision. The center will teach collision repair technicians how to efficiently repair existing vehicles, as well as adapt to the ever-changing repair procedures, technologies, and materials that will be required to fix the cars of the future.
“My vision is for a customer to contact a Toyota or Lexus dealership after a collision and for that dealership to be able to take care of them right away, whether it’s through Toyota’s Certified Collision Center Program, a Toyota Dealership Collision Center, or an affiliated independent collision center,” said Chris Chartron, Lexus Technical Training Manager at Toyota Motor North America, “We want to build trust with our customers. By making sure that our collision centers have the training to fix the vehicles right the first time, we’ll build that trust with our customers so they’ll come back to our
brand repeatedly.”
By making sure that our collision centers have the training to fix the vehicles right the first time, we’ll build that trust with our customers so they’ll come back to our brand repeatedly.
— Chris Chartron
THE MODERN COLLISION REPAIR EDUCATION
Collision repair is a constantly changing business and driver safety spends on well-trained technicians. Standards and repair procedures will continue to change with each new make and model released.



We have more and more safety systems, structural body changes, and advanced metals and alloys being used, compounded with a very litigious environment in the U.S.. Repairers need to follow the manufacturers’ repair procedures to ensure that every vehicle is returned to factory specifications.
— CHRIS CHARTRON
To ensure mastery of critical skills, training is equally divided between classroom and hands-on training—50 percent lecture and 50 percent lab. “We focus on getting the techs on the equipment so they can practice the skills we cover in class,” says Joe DiDonato, Technical Training Analyst of Quality Collision Repair and Refinish Training. “We’re strictly a training facility and all of our repairs are simulated—while the participants don’t repair customer vehicles, they do work on actual vehicles.” One look at the new Rancho Cucamonga Collision Repair Training Facility proves that Toyota is determined to offer the highest quality collision repair training in the industry. The sprawling facility includes:
- Office space, conference and lunch rooms
- A classroom that accommodates eight participants
- Paint prep and downdraft booth
- Paint spray booth
- Two in-ground lifts for steering/suspension and body frame classes
- A frame straightening machine for welded panel replacements
- Four welding stations for practicing and fine-tuning welding
WHY TOYOTA’S TRAINING IS UNIQUE
One of Toyota’s trademarks is setting new standards. “While all welding, frame straightening and painting equipment is the most current available, we don’t specify one brand of repair equipment because our students use a variety of equipment brands. Same with the paint,” continues DiDonato. “Every product we use is the most widely recognized in the industry. We don’t want to limit who can work on our vehicles. That’s also why our facility is open to all types of dealer sponsored independent shops.”
For example, there are five major paint companies recognized as industry leaders. “All four Toyota training centers use two or more of those brands,” says DiDonato.
All of this contributes to better, more efficient repairs. “We’re using equipment that more closely duplicates the factory process and puts less stress on the body,” notes DiDonato. “We can do things now that were impossible just 15 years ago—from paint that dries in 15 minutes to 8,000 grit sandpaper that basically eliminates the need for rubbing compound.”
Five brand new Techstream diagnostic scan tools complement all of the new technology. “Each of our training centers conduct a pre- and post-scan on every vehicle” says DiDonato. “We train technicians how to connect and read the scan tool to see if there are any diagnostic codes before or after repairs.” While Toyota dealers use Techstream, Techstream Lite is available to independent shops. Both tools are specific to Toyota/Lexus vehicles. Technicians can then find everything from A to Z on Toyota’s Technical Information System (TIS) to complete repairs.
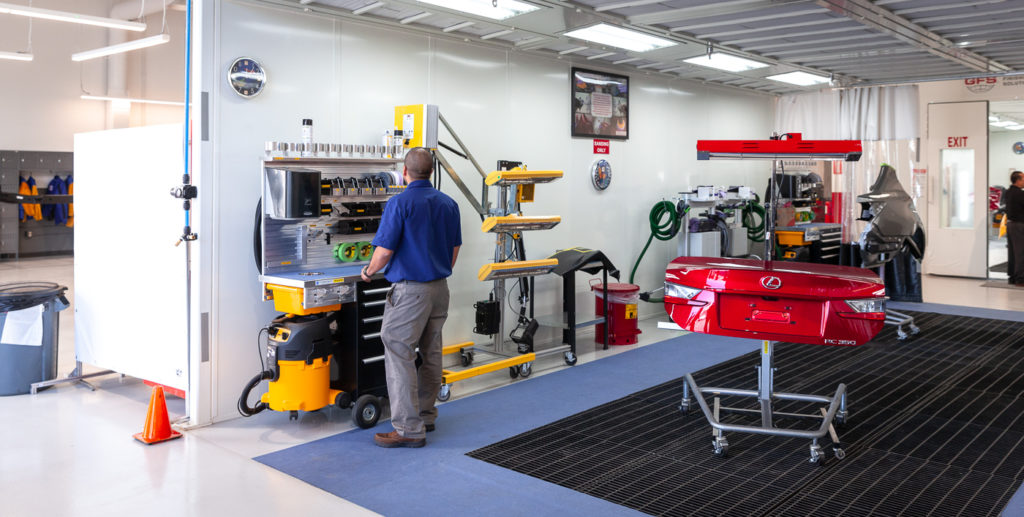
THE RANCHO CUCAMONGA FACILITY IS OPEN FOR CLASSES!
“Multiple courses are available for Collision Refinish, Repair, and Mechanical Technicians,” said Chartron. “We’re constantly providing feedback on our repair procedures to Toyota and continuously looking at new courses to ensure that technicians have the information they need to repair our vehicles correctly.” Training is divided into three courses of study: paint, body, and electrical/mechanical. They are open to the following:
- Collision repair and refinish professionals currently employed by a Toyota or Lexus dealer-owned repair facility
- Independent affiliate repair and refinish professionals sponsored by a Toyota or Lexus dealer
“Toyota would like its customers to bring their vehicles to one of the roughly 200 Toyota Certified Collision Centers that we have across the country, because we know they have the equipment and training to do the job right,” said Chartron. “But we also know that’s an unrealistic expectation to reach all customers with just those shops. That’s why we feel it’s so important to offer comprehensive collision repair courses to our sponsored independent repair shops. Customers will benefit from a better repair experience and can rest assured that their vehicle has been restored to factory condition.”
FROM BUSINESS CASE TO REALITY
A Collision Training Dream Come True. The California Collision Training Center began in 2016 as a business case. “We could have just shut down the old training center in Torrance and moved on, but that wouldn’t have been the right move for our customers,” said Chartron. “We want to make sure that our customers are experiencing the best customer service even after a collision. By creating this training center and providing all collision repair centers with the proper training and hands-on experience, we can ensure that our customers’ vehicles are being repaired correctly the first time.”
Chartron and his team worked with IT, real estate, and executive management to get the project off the ground. The team decided on a building in the Inland Empire with easy access to freeways and to the Ontario Airport that’s near other Toyota facilities, like the North American Parts Center in Ontario.
Project manager Kristen James worked with Chartron and a team of architects to design the facility. No detail was too small to plan, from the number and location of repair bays to the specifics of the paint booth. The result is a well-designed, high tech training facility that will prepare technicians to provide the highest quality repairs in the industry.
FOR COURSE DETAILS, sponsorships or to sign up, go to http://www.crrtraining.com.